The majority of the car’s core structure was solid, unfortunately the primary exception was a section on the inside of the driver’s side C pillar. A highly awkward area that isn’t reproduced, I had no good options other than reproducing the part somehow. Due to the mildly complex curves on the flanges I knew I didn’t own the correct tools to fabricate a passable patch panel myself without creating many tiny pieces and welding them all together. Instead I decided to give the CAD-based laser cutting another go.
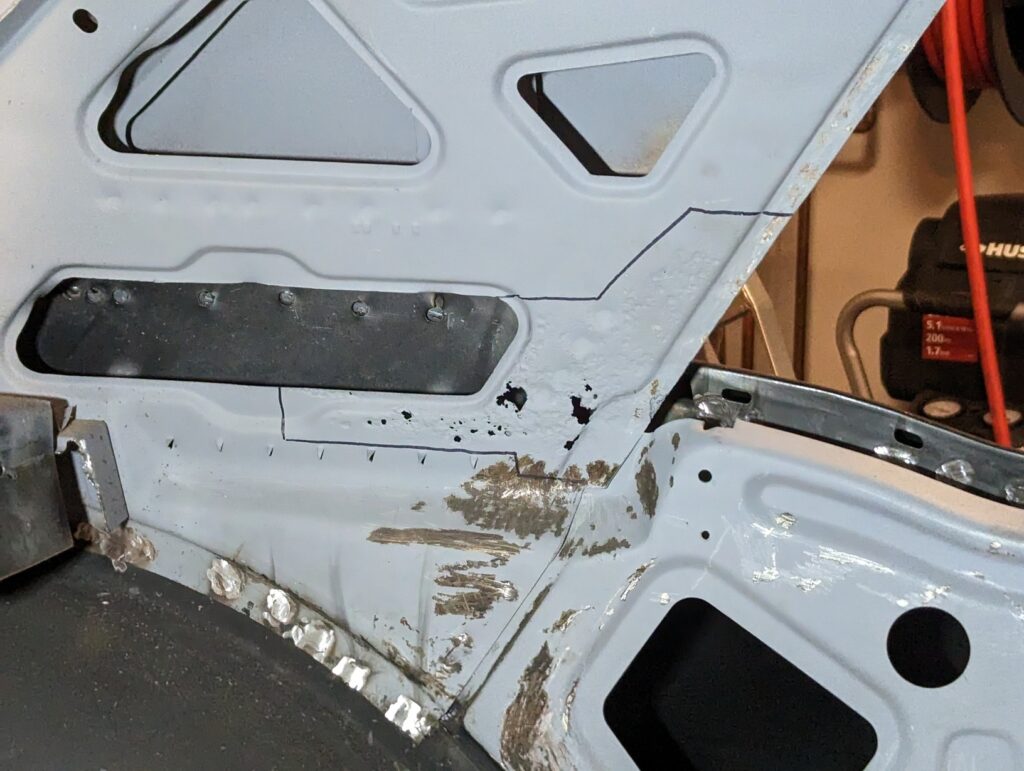
The first step was to cut out the rusted area so that I could take measurements while creating it in CAD.
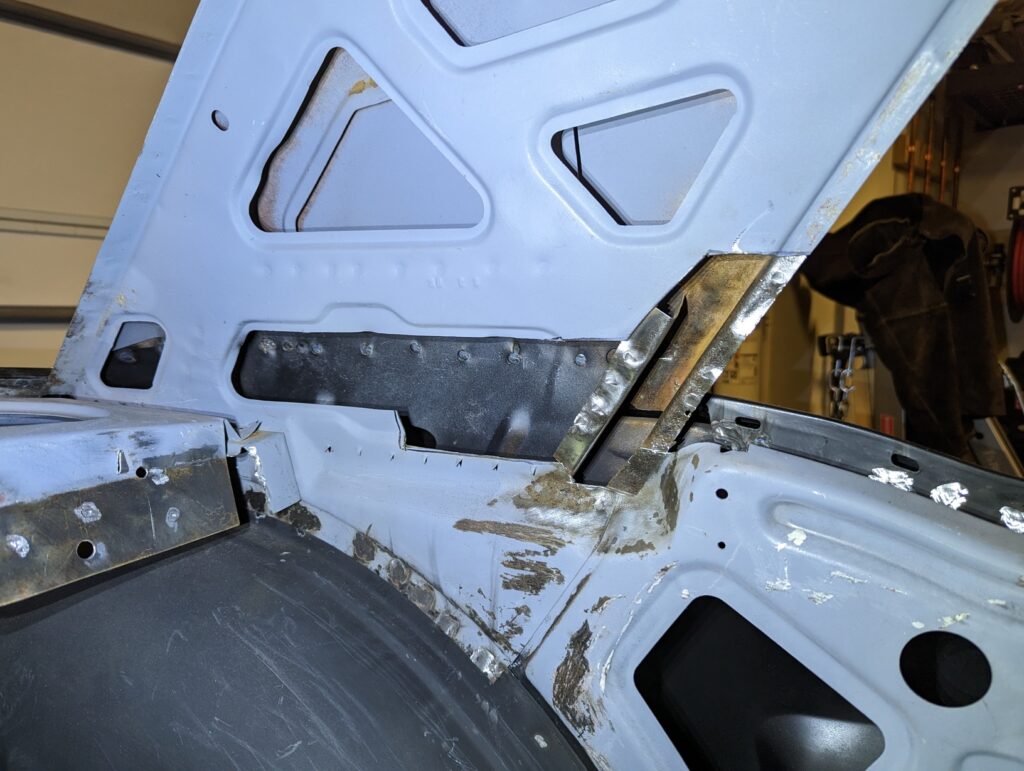
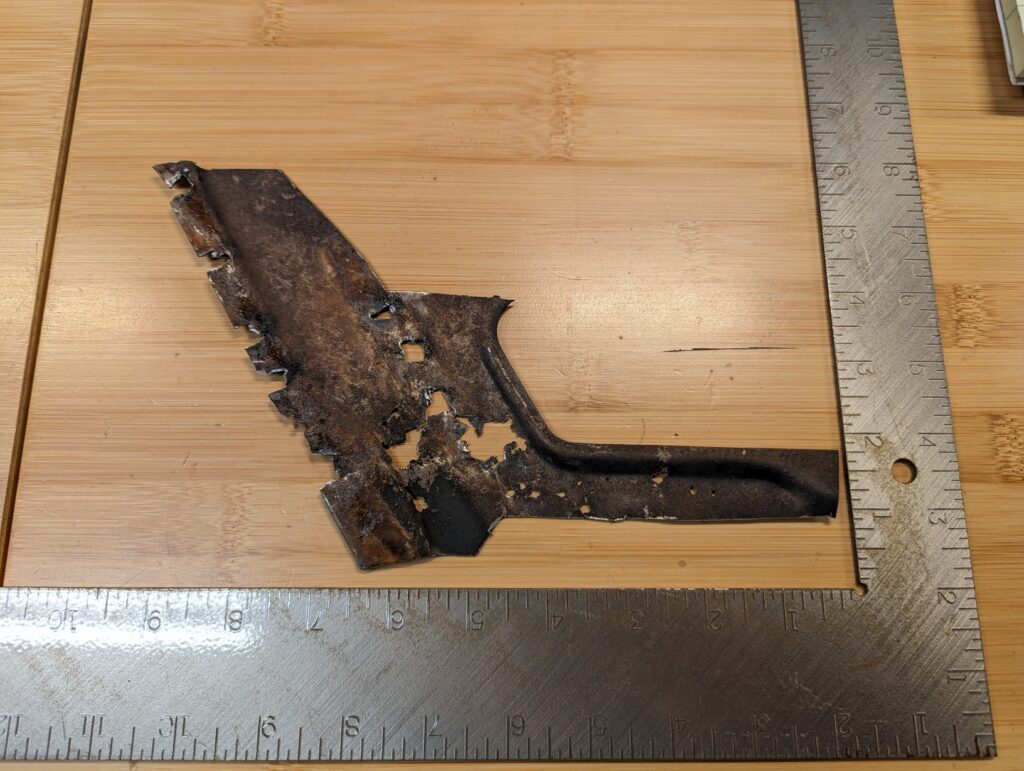
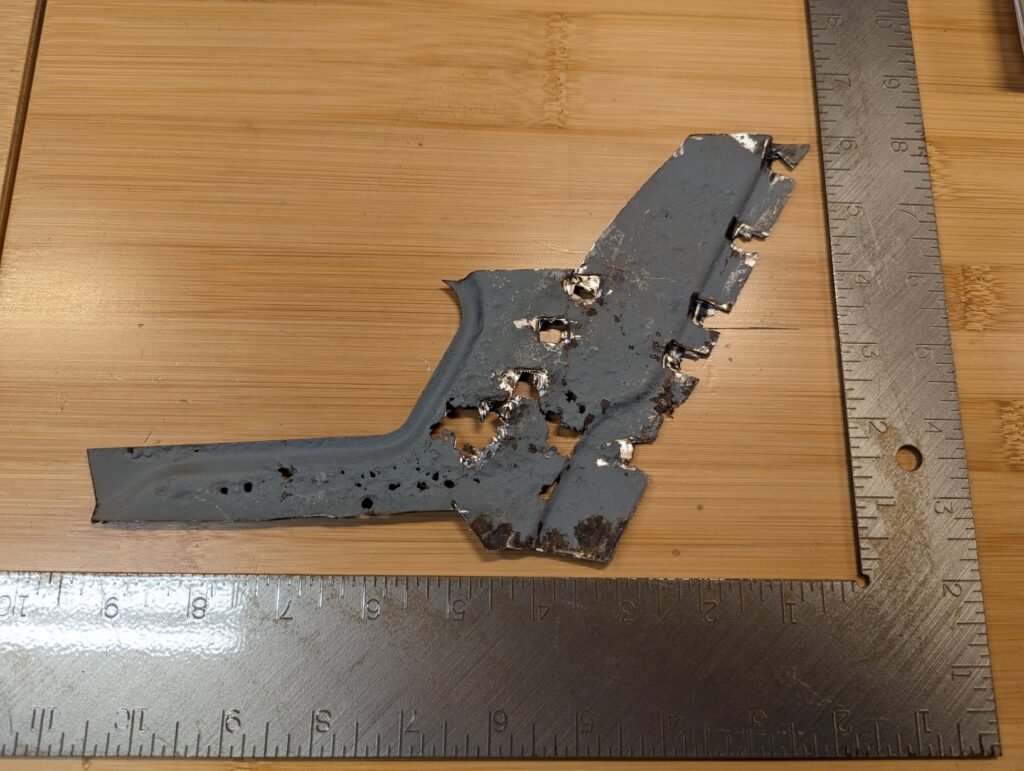
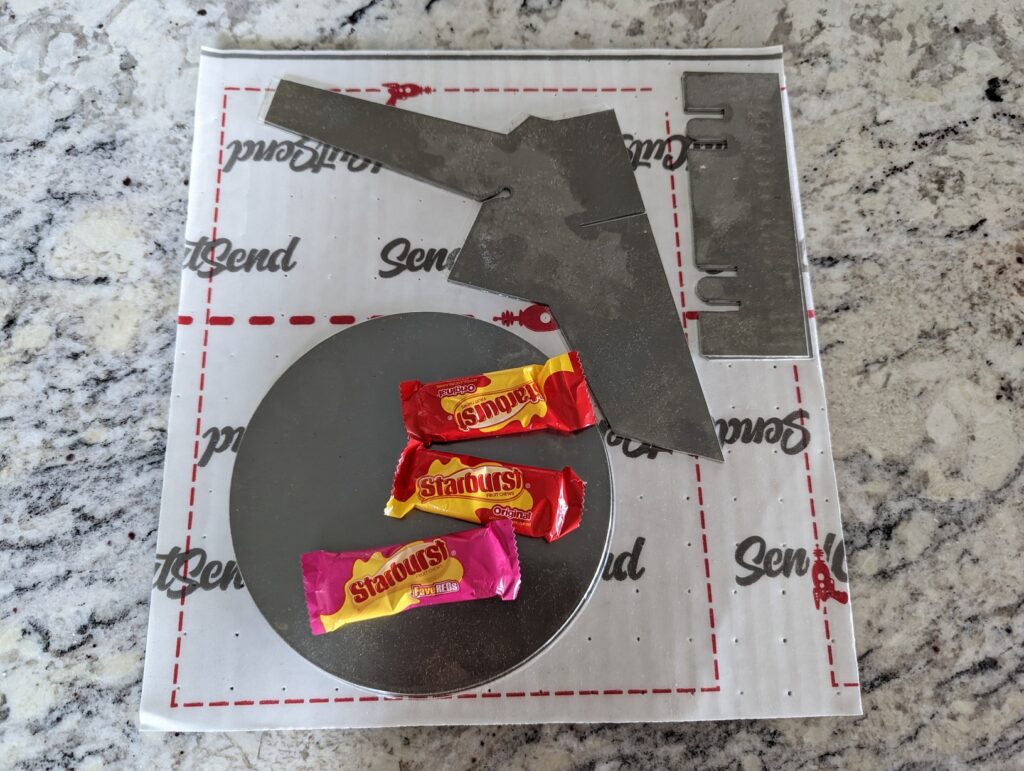
The laser cutting supplier wasn’t able to do the bends on this piece due to the limited space between the compound bends and the various angles of the flanges.
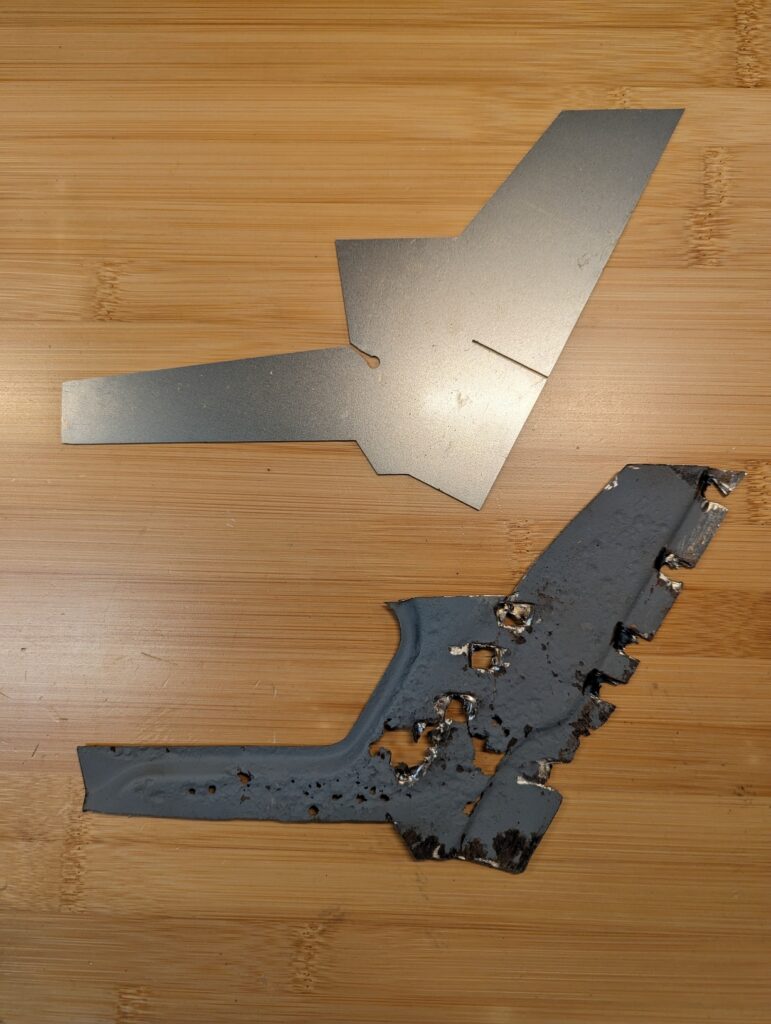
In my CAD reproduction I simplified some of the curves along the left side of the piece to make it easier for me to bend in my garage with my limited toolset.
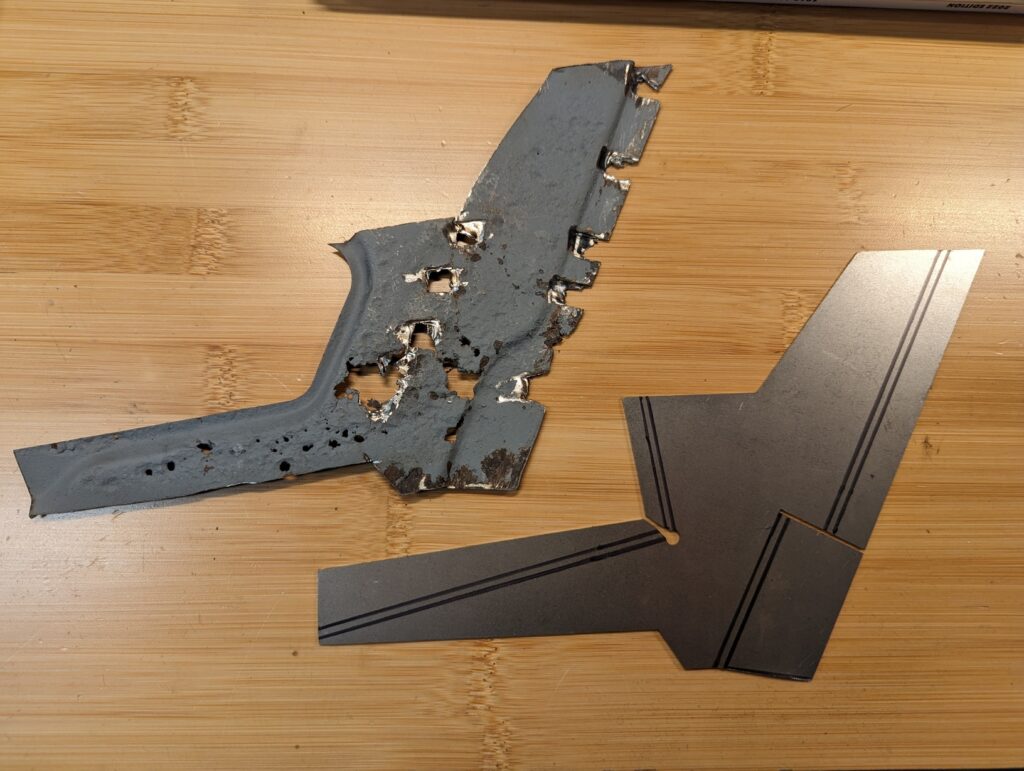
I ordered multiple copies of the piece both as insurance against any required retries and to meet the order minimum for the service. Each copy only cost me a couple dollars.
The one on the far right in the next picture is post-bending via bench vice, hammer, and dolly.
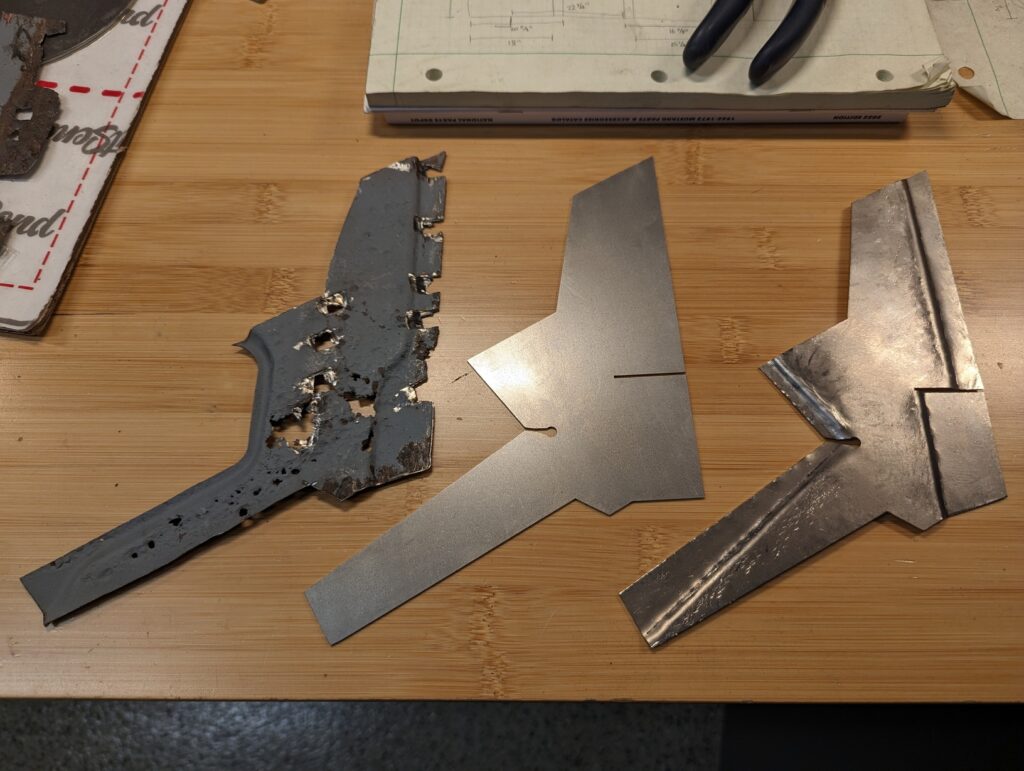
After cleaning up the rust as best I could and spraying in a coat of rust encapsulator I went ahead and coated the back side of the patch panel as well.
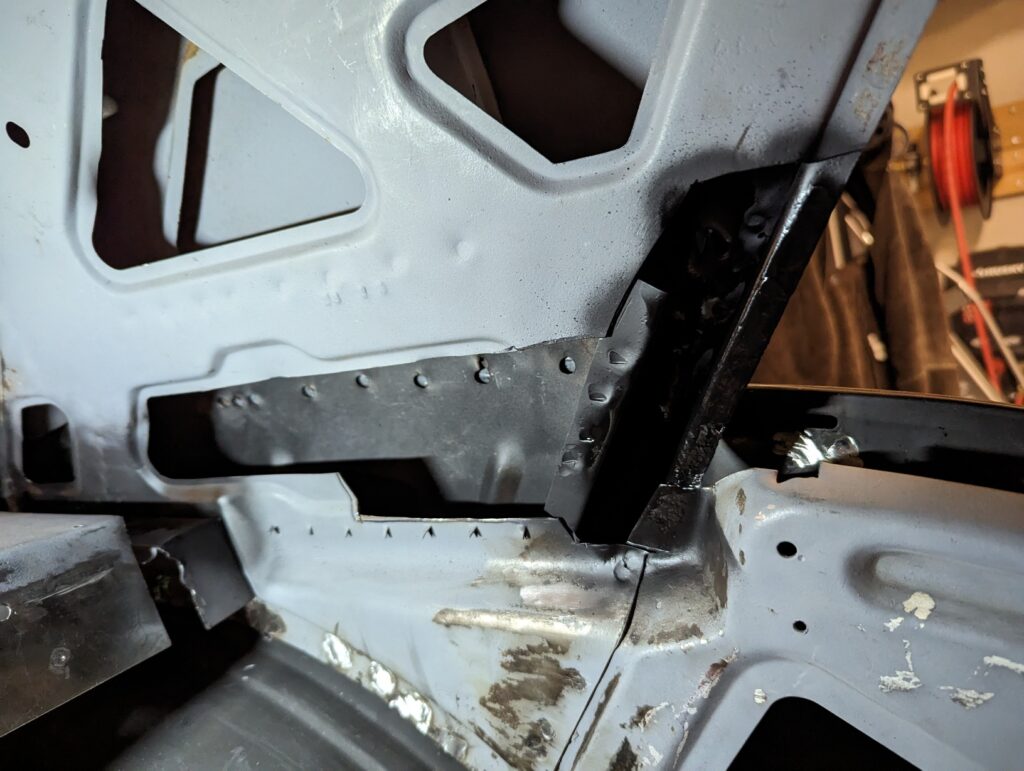
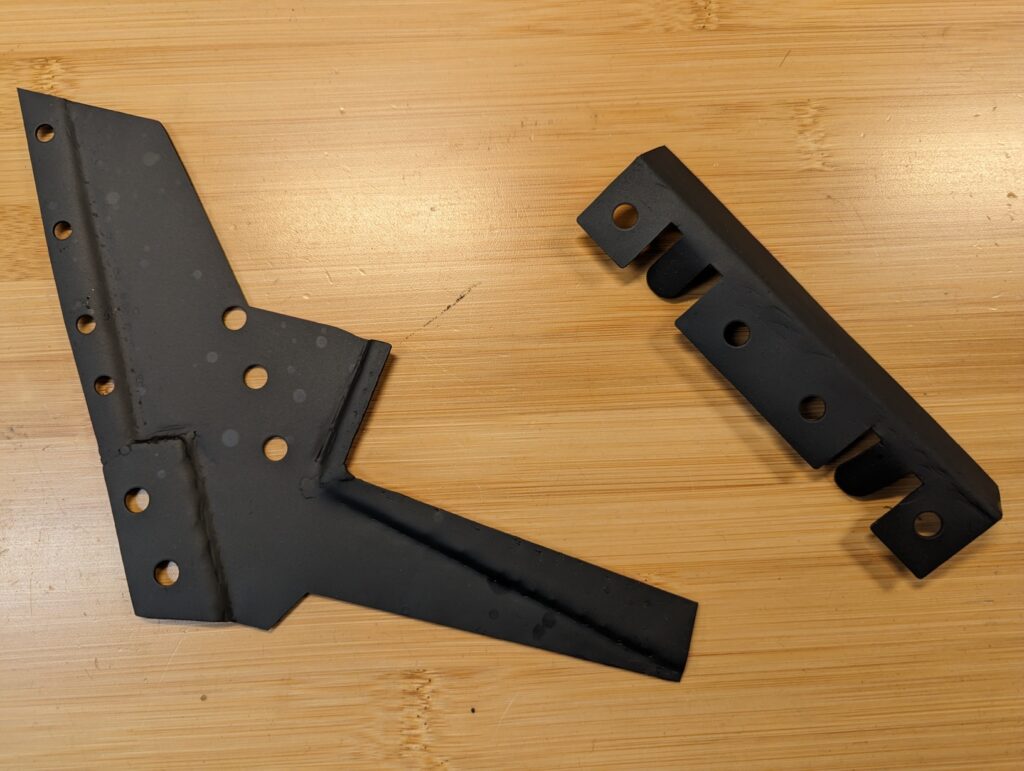
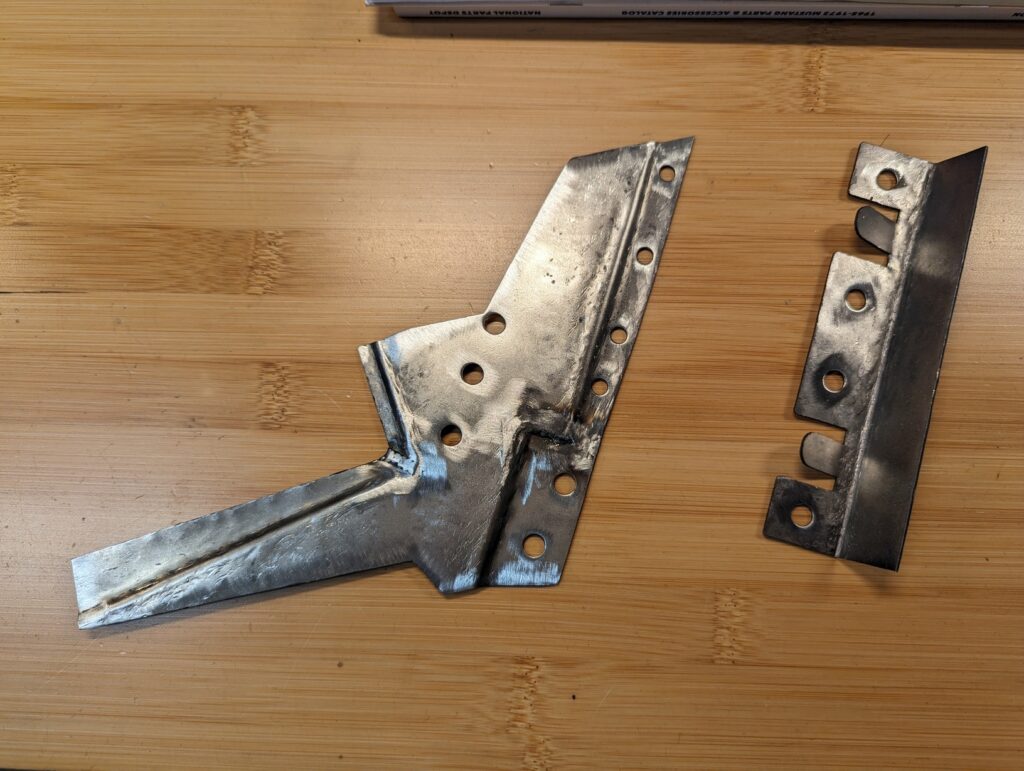
Time to weld it in!
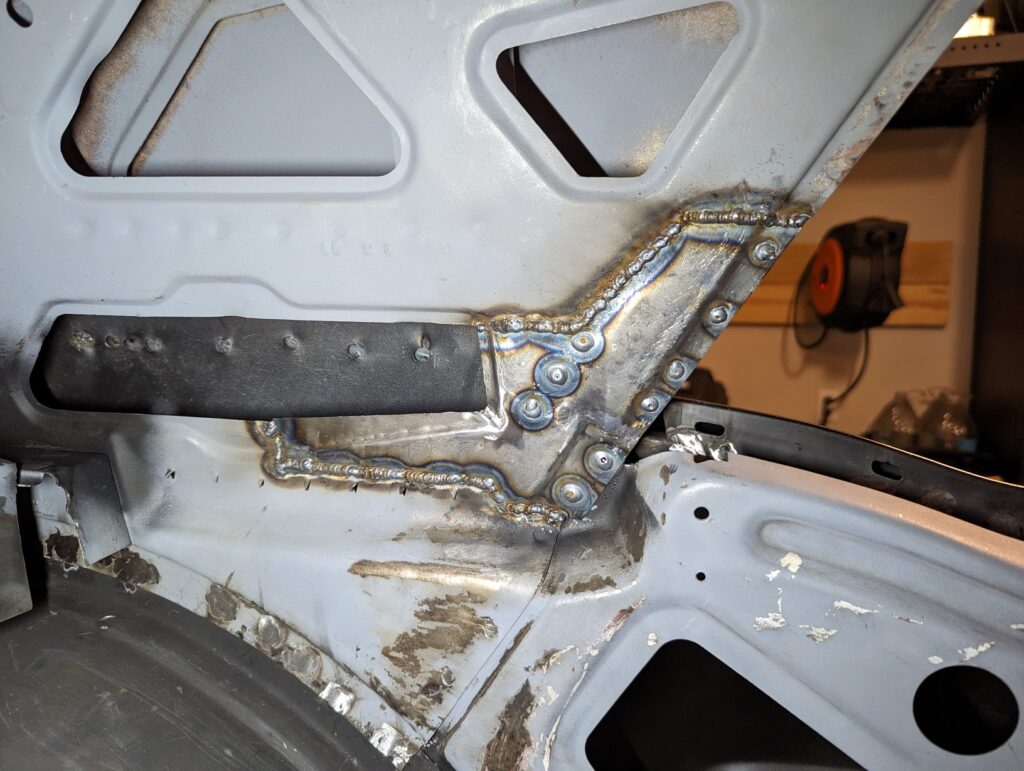
After some grinding I was pretty happy with how it turned out. It’s not a perfect match for stock but it’s reasonably close and will never be visible anyway thanks to the headliner covering the entirety of the C pillars.
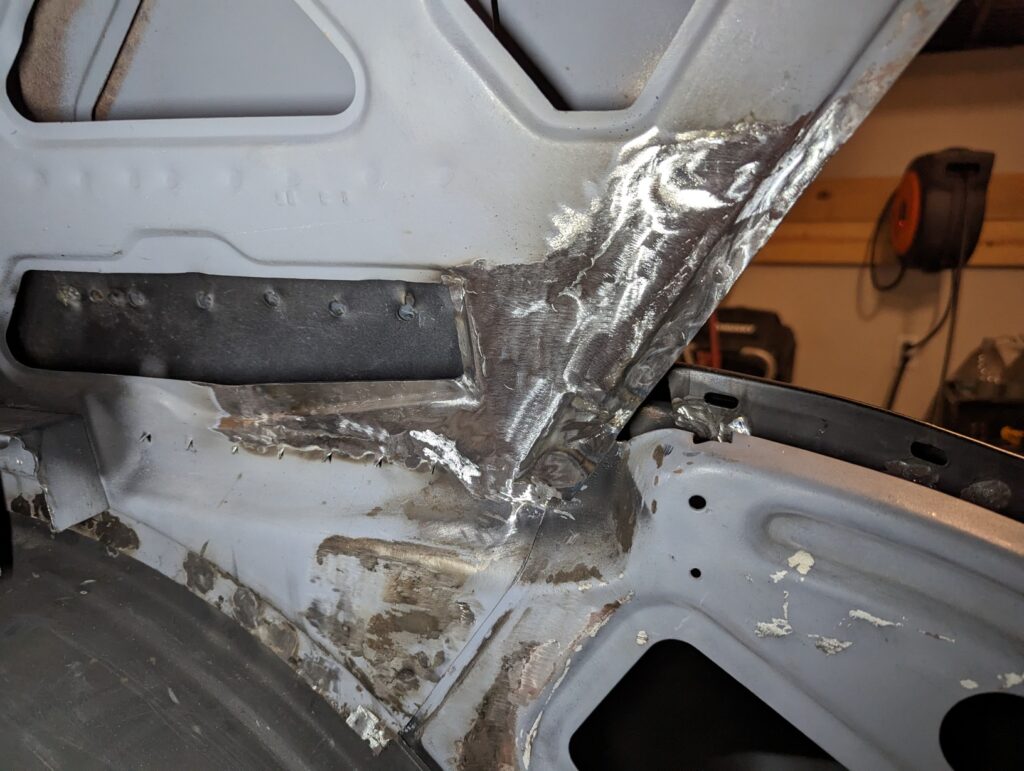
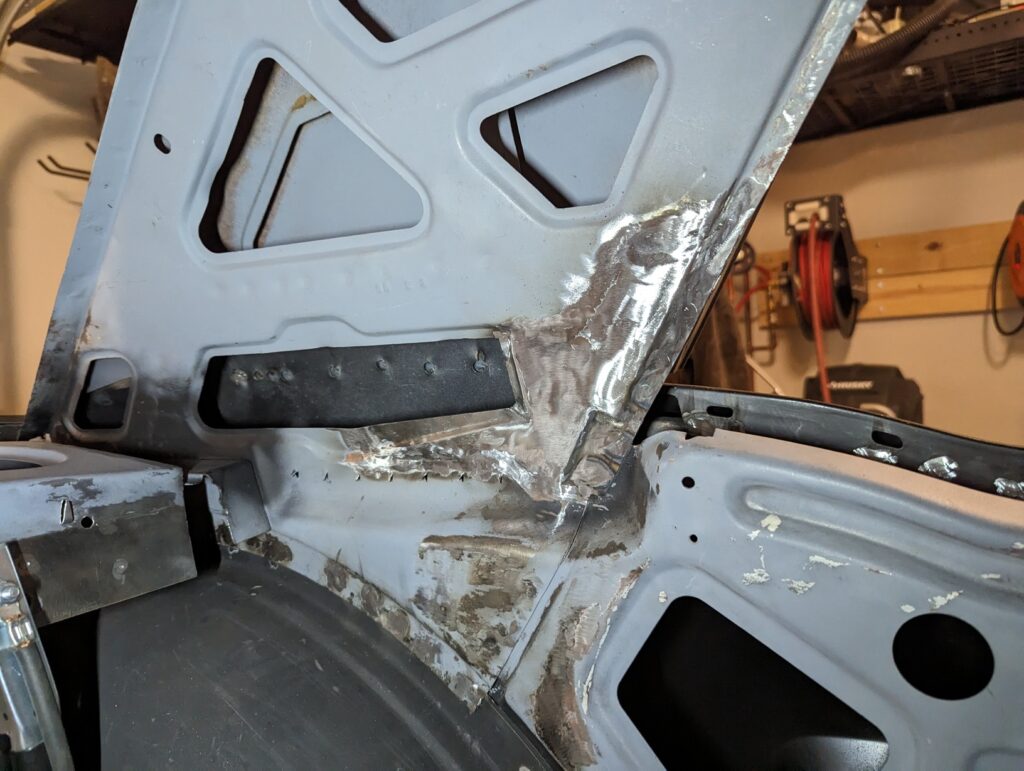