The first order of business was to mock up the entire cowl and install the wiper motor assembly to ensure that everything was lining up as expected. It appeared that the front of the upper cowl wanted to sit back a fraction of an inch further on the driver’s side than it did on the passenger’s side but all of my measurements were still coming out as expected, indicating that it was actually the lower cowl sticking out a bit further on the driver’s side which is of no real consequence. You can see it if you look closely at the leading corners of the cowl assembly in the next few photos.
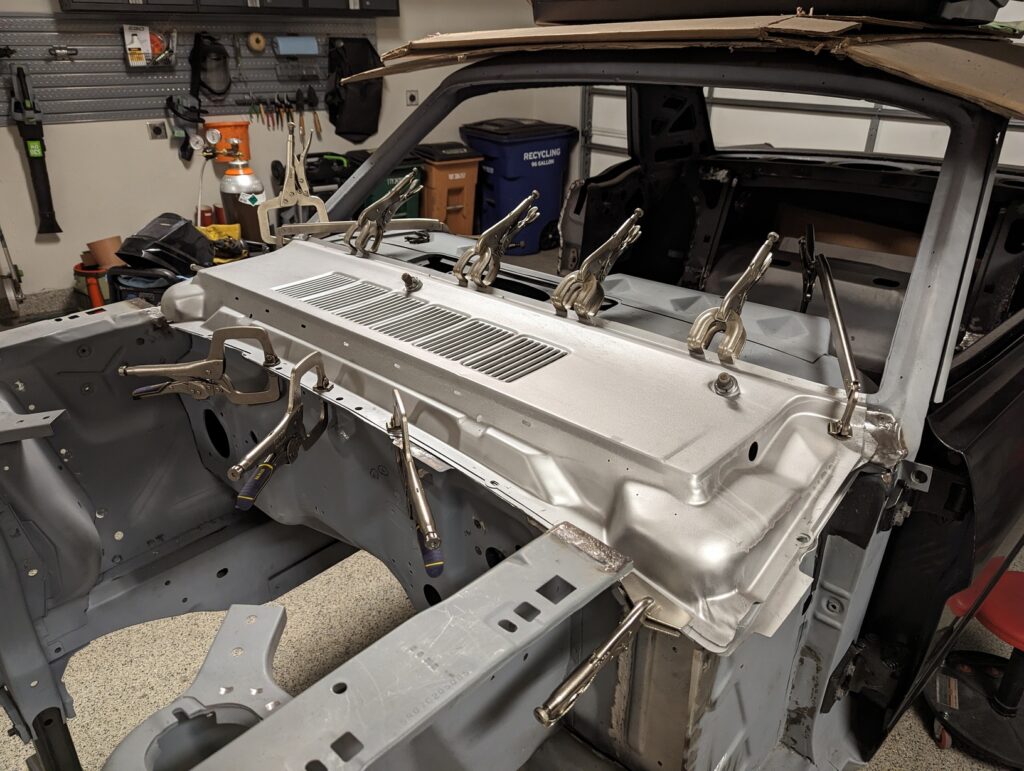
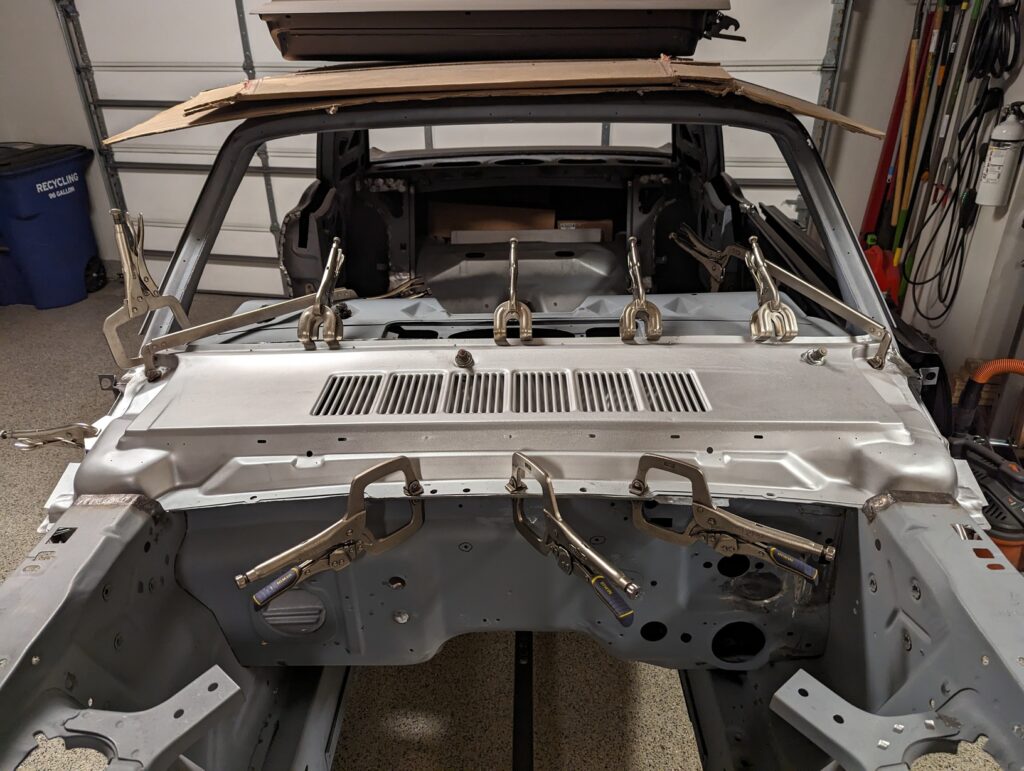
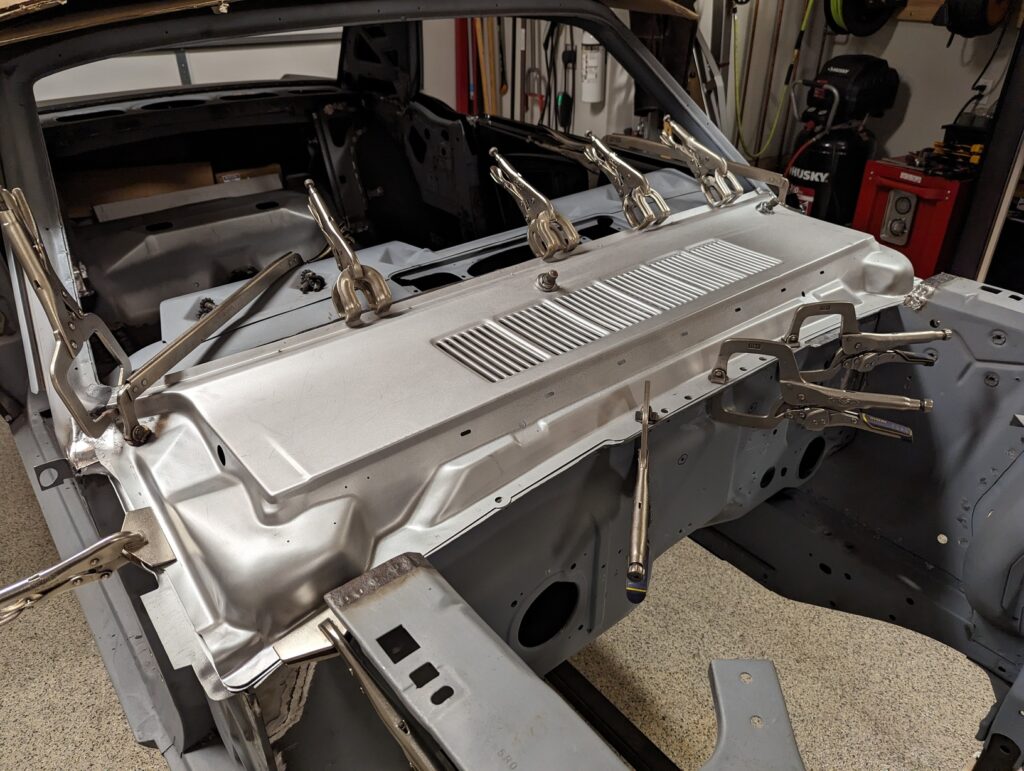
With the dry fit done I used the original lower cowl as a reference for where to drill out the holes for the spot welds.
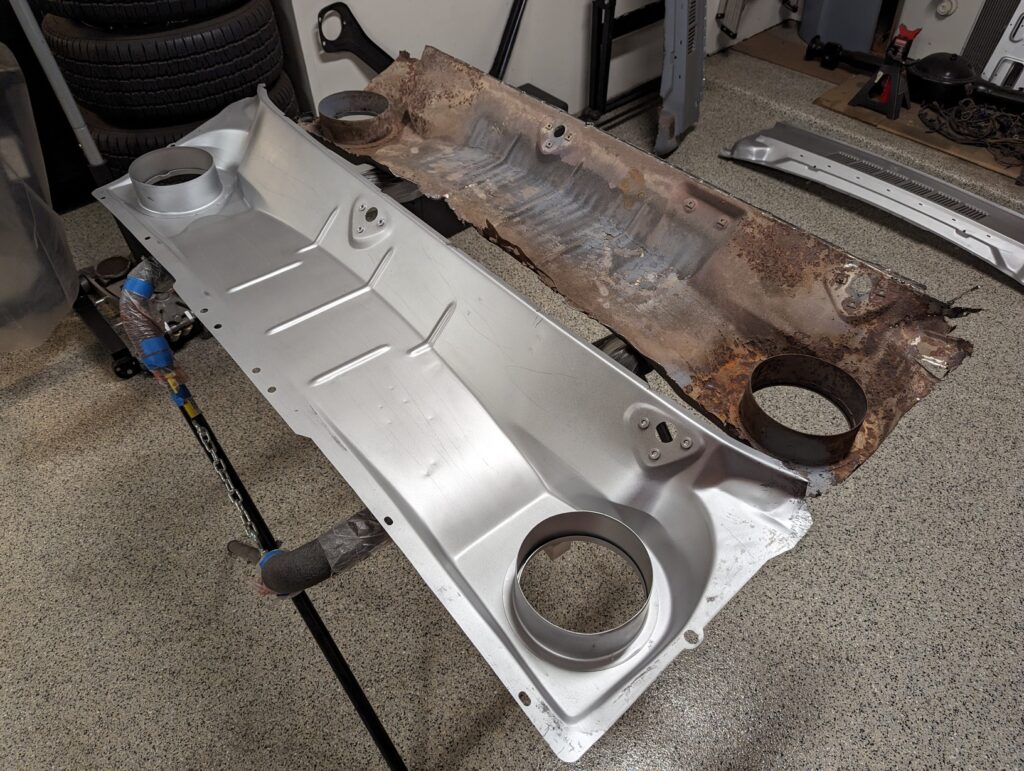
With the holes all drilled it was a matter of clamping, grinding away the paint on the mating surfaces of the spot welds, and welding them up.
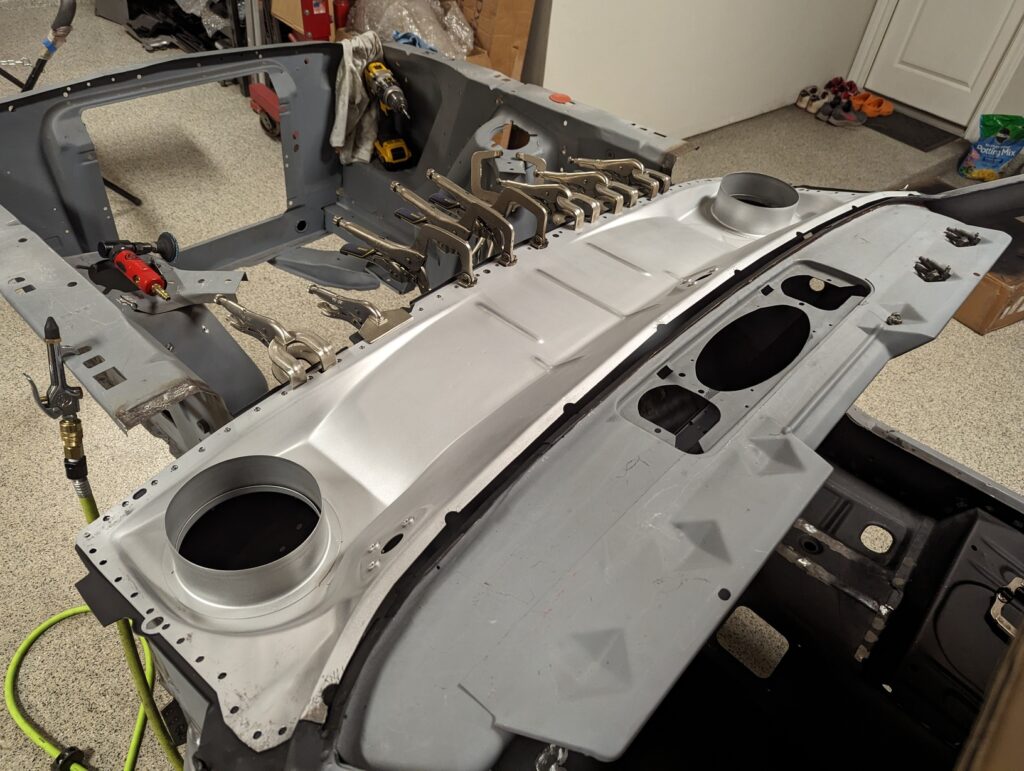
The base of the A pillars is where the reproduction cowl didn’t quite align perfectly, it took some creative clamping and extra sheet metal screws to pull everything flush for welding.
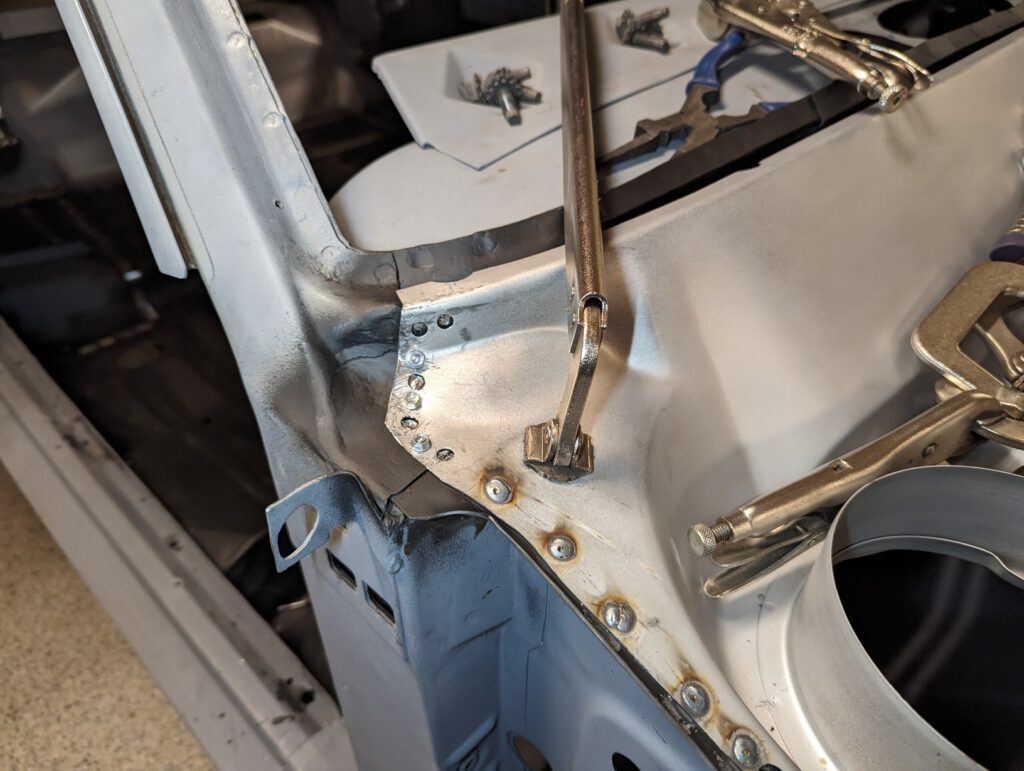
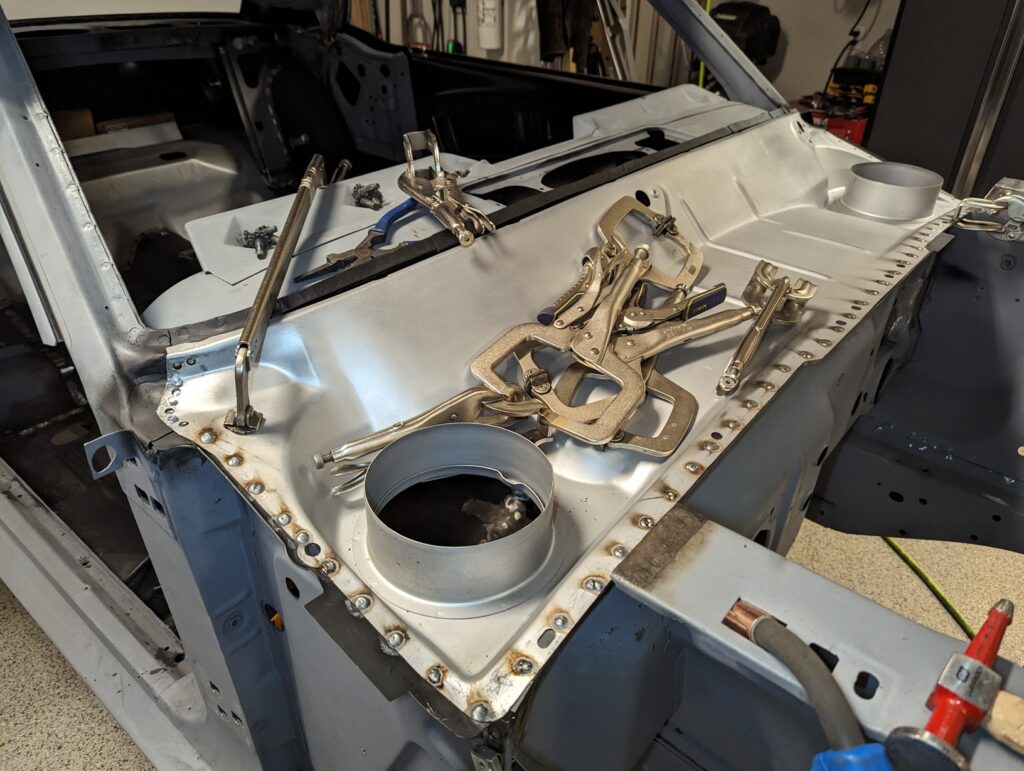
Skip forward several hours and the lower cowl was in!
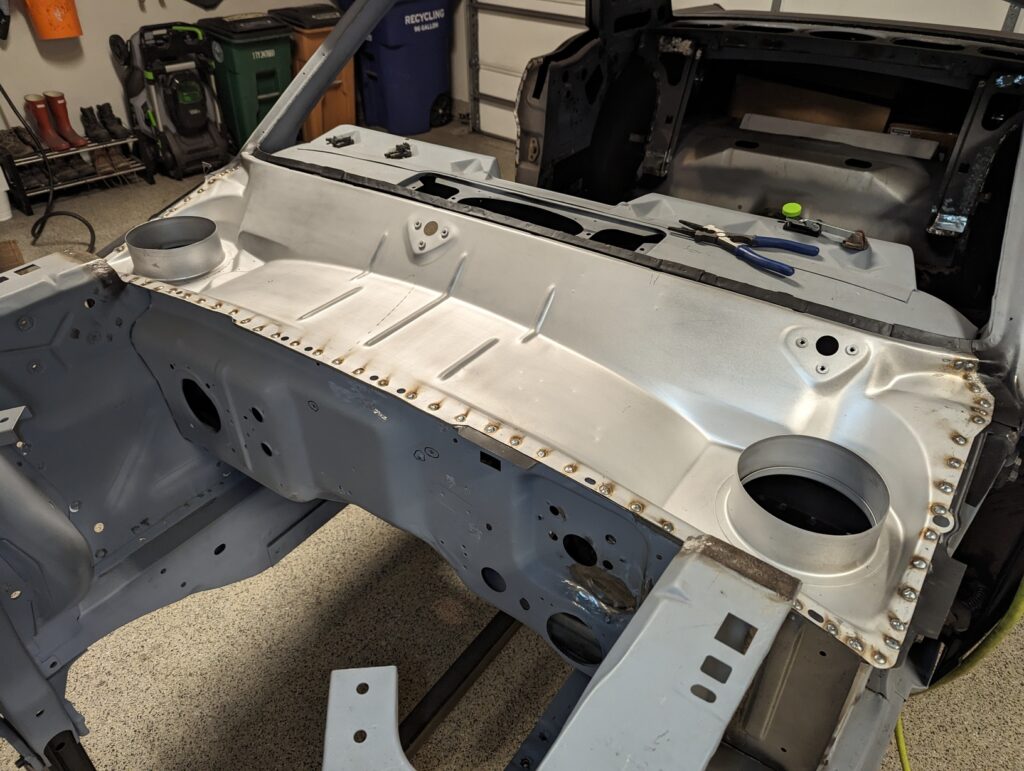
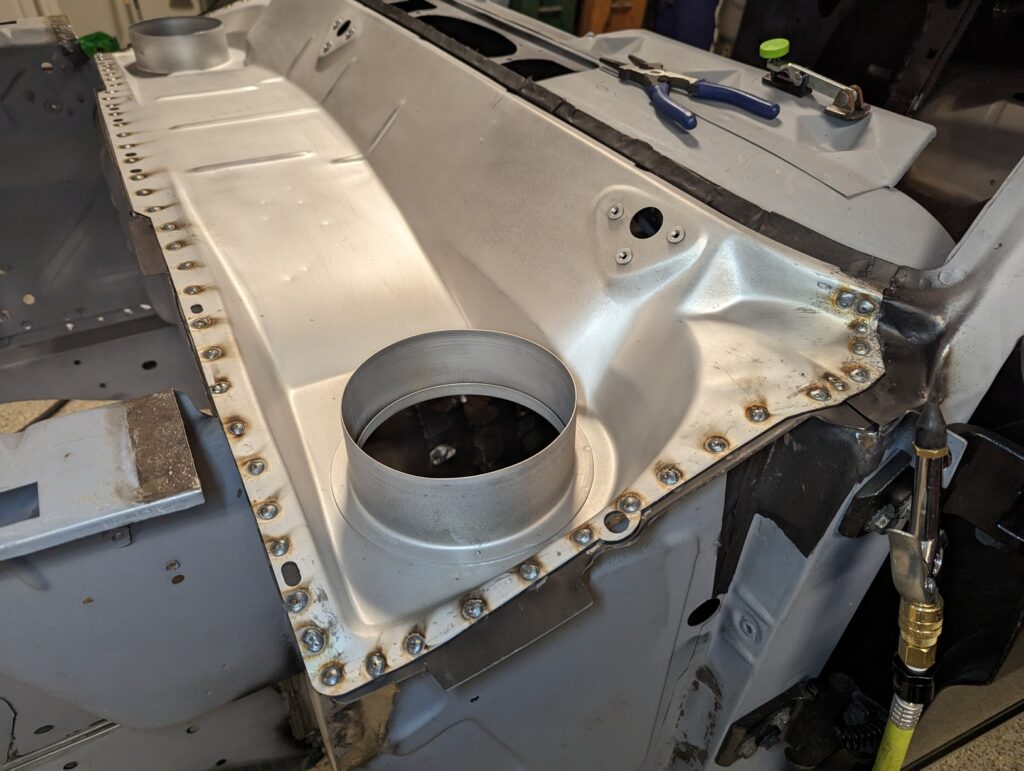
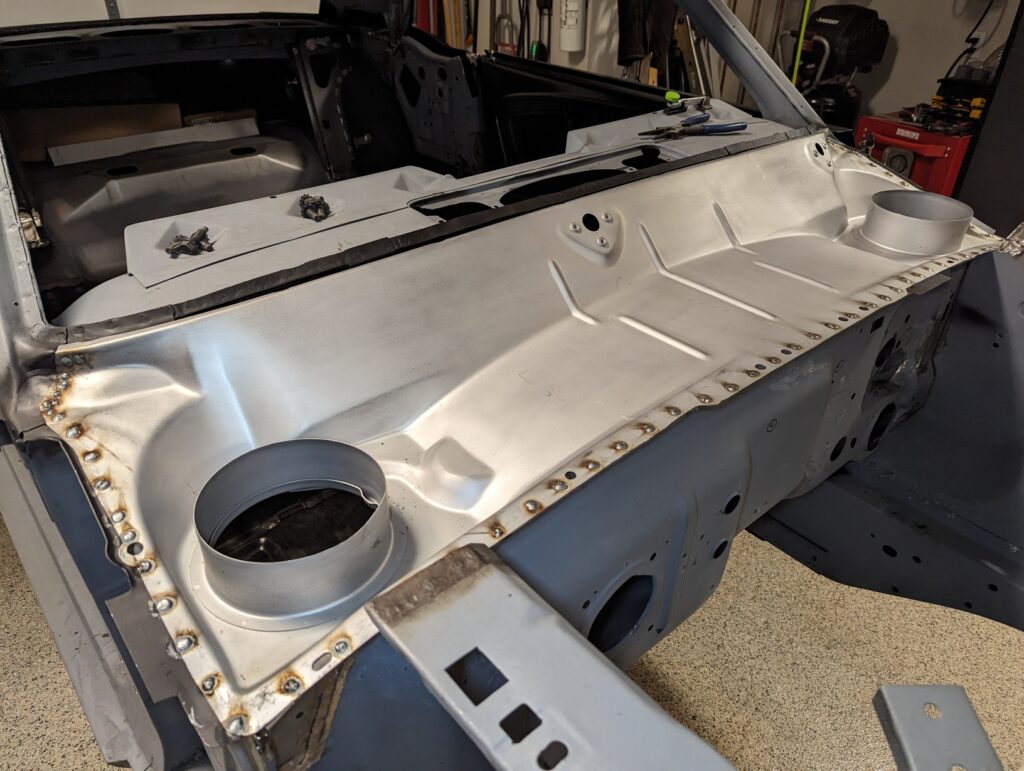
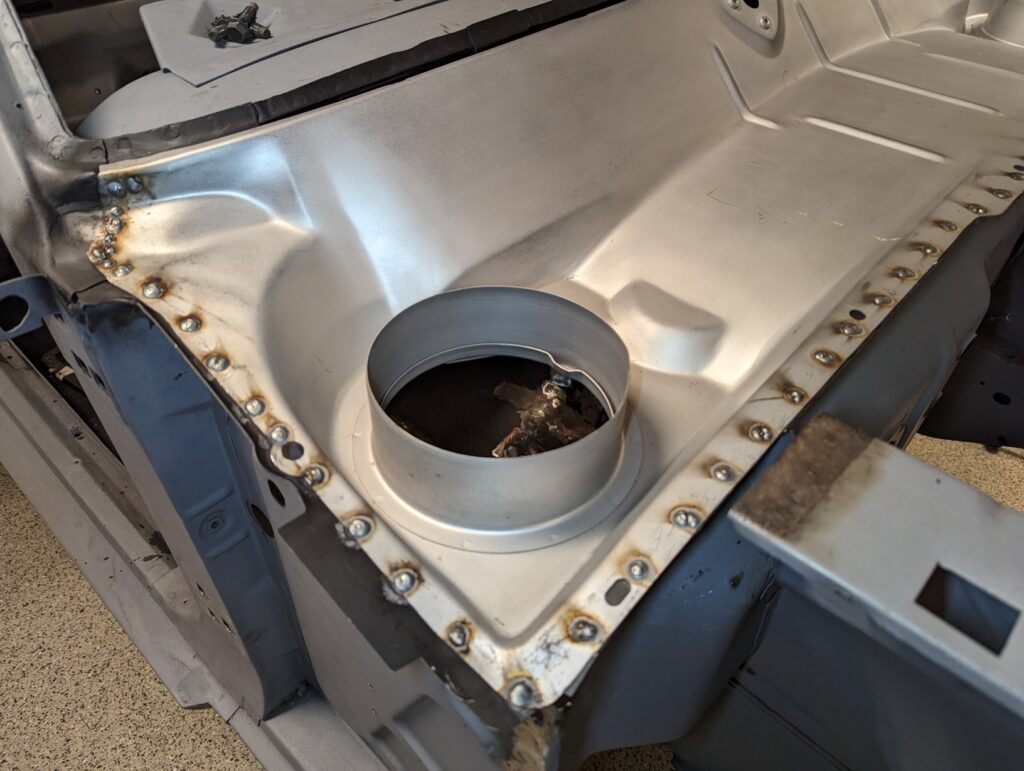